Are you curious about the heart of a wind turbine and how it transforms the gentle breeze into a source of power? The wind turbine gearbox, often unsung, plays a critical role in this process, facilitating the efficient generation of electricity from the kinetic energy of the wind.
The mesmerizing dance of wind turbines, with their sweeping blades, has become a familiar sight across the globe. Their elegant form belies the complex engineering that enables them to capture the wind's energy. At the core of this technology lies the gearbox, a vital component that bridges the gap between the slow, powerful rotation of the turbine blades and the high-speed rotation needed to generate electricity efficiently. The blades, the hub, and the main shaft of a wind turbine harness the kinetic energy of the wind and convert it into rotational mechanical energy. This mechanical energy is then channeled through the gearbox.
Wind turbine gearboxes are not merely cogs in a machine; they are intricate systems designed to withstand immense forces and operate under demanding conditions. These gearboxes are developed for standard industrial applications, but there was no customizing for special wind turbine behavior. The main parts of a wind turbine gearbox include gears, with the use of bearings and shafts, the gears are meshed together, enabling the system to handle high loads and provide reliable performance.
- Easy Cute Penguin Drawing Ideas Learn To Draw Fun Penguins
- Unveiling Madame Rcamier Life Art Legacy Discover Now
The main function of the gearbox is to increase the rotational speed of the turbine blades. For example, to generate electricity in the case of a 1 MW wind turbine, the gearbox increases the rotation speed of the blades from 15 to 20 rotations per minute up to the about 1,800 rotations per minute that is required. This speed increase is crucial because it allows the generator to operate at its optimal efficiency. Approximately 75% of all wind turbines are based on geared designs, demonstrating the widespread reliance on gearboxes in the industry. However, even if the solution without gearbox is used by several manufacturers (e.g., the Goldwind 2.5 PMDD, Enercon models, etc.), the majority of makers decided to include it.
Feature | Description |
---|---|
Definition | A wind turbine gearbox is a mechanical component designed to increase the rotational speed of the turbine blades, converting the low-speed, high-torque input from the blades into a high-speed, low-torque output suitable for the generator. |
Function | Primarily to step up the rotational speed. For example, a gearbox might increase the blade rotation from 15-20 RPM to around 1,800 RPM, which is necessary for the generator to function optimally. |
Key Components |
|
Types of Gear Systems |
|
Material and Design | Gearboxes are typically constructed from high-strength steel alloys to withstand the extreme stresses and wear they endure. These steel grades have low carbon and high chromium and molybdenum content to increase the maximum toughness. Design considerations include gear ratio, gear geometry, and lubrication systems to ensure optimal performance and longevity. |
Impact of Gear Ratio | Gear ratios can also influence the noise levels generated by wind turbines. Higher gear ratios, which result in increased rotational speeds, can lead to higher noise emissions due to the greater meshing frequency of the gears and the increased aerodynamic noise from the generator. |
Reliability and Maintenance | Gearboxes are subject to significant stress, and their reliability is critical for the overall performance of the wind turbine. Fatigue failure of gear transmission is one of the key factors that restrict the performance and service life of wind turbines. One of the major concerns in gear transmission under random loading conditions is the disregard of dynamic fatigue reliability in conventional design methods. Regular maintenance, including lubrication and inspection, is essential to prevent failures. |
Failure | The weakest link of a size wind turbine has been utility their gearbox. As turbine sizes increased, the design gearboxes able of. Higher loads would slowly damage bearings, then gears, and eventually require a gearbox swap. 3.1.1 wind turbine gearbox failure. |
Cost Implications | The costs associated with securing a crane large enough to replace the gearbox and the long downtimes associated with such a repair affect the operational profitability of wind turbines. A simple gearbox replacement on a 1.5 MW wind turbine may cost the operator over $250,000 (Rensselar, 2010). |
Recent Research | Recent studies have focused on gear contact damage failure mechanisms. Zhus group has done a lot of research on gear contact damage. |
The relentless forces at play within a wind turbine gearbox are substantial. For instance, the constant pounding of the wind on the rotor and main shaft of older designs slowly hammers away at the gearbox. This constant exposure to stress and wear makes the gearbox a critical component in terms of maintenance and potential failure. Therefore, the condition of a gearbox shouldnt be neglected, lest the operator faces grave consequences.
Gearboxes play a crucial role in horizontal axis wind turbines (HAWTs), which are the most common type. For this wind turbine type, the blades rotate by a shaft connected via a gearbox to the generator. 7.1 shows a schematic layout of the main subsystems found in a typical HAWT. The gearbox is coupled to the rotor through. The gearboxs primary function in a HAWT is to step up the relatively slow rotational speed of the rotor to a higher speed suitable for the generator. Horizontal axis wind turbines (HAWT) with power ratings in excess of 500 kW have a dedicated ISO/IEC standard for gearbox design [2].
- Dennis Rodmans Lakers Era Stats Untold Stories
- Daniel Rohrbough A Columbine Tragedy Remembered Learn More
Given the high stresses involved, gearbox failures can be costly. The costs associated with securing a crane large enough to replace the gearbox and the long downtimes associated with such a repair affect the operational profitability of wind turbines. An accurate prediction of the product life of drivetrains is crucial for safe and reliable operation of wind turbines. It is reported that the failure rate of gearboxes is higher than other wind turbine components. A simple gearbox replacement on a 1.5 MW wind turbine may cost the operator over $250,000 (Rensselar, 2010). The impact of gear ratio on wind turbine noise levels is also an important consideration. Gear ratios can also influence the noise levels generated by wind turbines. Higher gear ratios, which result in increased rotational speeds, can lead to higher noise emissions due to the greater meshing frequency of the gears and the increased aerodynamic noise from the generator.
Planetary gear systems are widely used in wind turbines due to their ability to convert the low rotational speed of the turbine blades into the appropriate speed for the generator. In a planetary gearset, a couple of advancements can reduce rolling element maintenance and handle more load. Having delivered over 90,000 main gearboxes and 450,000 pitch & yaw gearboxes worldwide, established as a trusted partner for those defining the future of wind energy. With the use of bearings and shafts, the gears are meshed together, enabling the system to handle high loads and provide reliable performance.
The design and operation of wind turbine gearboxes are continuously evolving, with research and development focused on improving their reliability, efficiency, and lifespan. Reducing the cost of energy (COE) has become one of the main research drivers in wind energy. Various issues, such as overweight structure or insufficient fatigue reliability, require continuous experimental evaluation of wind turbine gearbox structural models using fiber optic strain sensors.
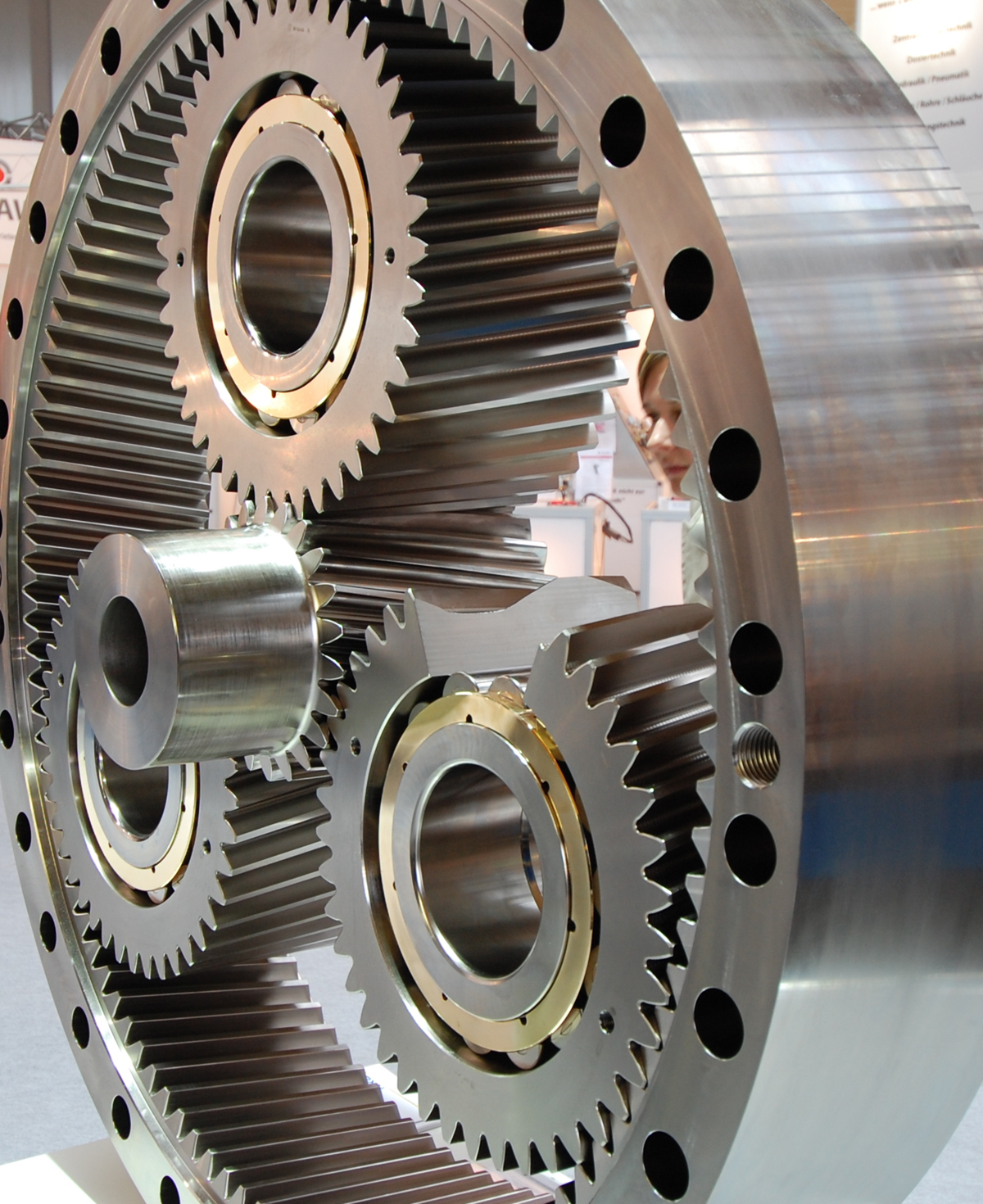


Detail Author:
- Name : Mrs. Audrey Schaefer III
- Username : dchamplin
- Email : era32@hotmail.com
- Birthdate : 1977-04-19
- Address : 639 Larkin Alley Reannahaven, AL 30000
- Phone : 1-754-669-2903
- Company : Stanton, Buckridge and Block
- Job : Civil Engineer
- Bio : Officia autem suscipit maiores aut vel quaerat. Eveniet officiis cum porro similique dolorem. Vel asperiores facere exercitationem cupiditate quo.
Socials
instagram:
- url : https://instagram.com/markus5010
- username : markus5010
- bio : Nisi dolorum ut quis dolore. Ut tempore ut est. Iste sit incidunt et vitae.
- followers : 6389
- following : 1175
facebook:
- url : https://facebook.com/markus_grady
- username : markus_grady
- bio : Dignissimos ducimus unde laudantium nam.
- followers : 3065
- following : 927